Armorit offers a comprehensive suite of technical and support services. All services are supported with ISO compatible documentation, filing and reporting. We are committed to customer satisfaction and excellence.
Product Assembly and Delivery
Armorit provides low to medium volume assembly for systems, sub-systems or components; providing finished goods or sub-assemblies to our customers. In addition, Armorit uses custom assemblies and prototypes to support its product development activities.We Specialize In
- Specialty vehicle sub-systems
- Personal protection devices
- Mechanical systems and enclosures
- Cables and wiring harnesses
- Transportation systems
We offer product delivery options ranging from drop shipments to line side delivery.
Project Management
The Armorit Project Management focus is to support our customers in a structured approach and execution of the tasks necessary to achieve their business objectives. The prime directive of project management is to be on time, meet quality objectives, and control the project within the budget. These activities form the classic time, quality and cost triangle.Project Management is composed of several different types of activities and are assessed continually throughout the project life cycle:
- Planning the work or objectives
- Analysis and design of objectives
- Assensing and mitigating risk
- Estimating resources
- Allocation of resources
- Organizing the work
- Aquiring human and material resources
- Assigning tasks
- Directing activities
- Controlling project execution
- Tracking and reporting progress
- Analyzing the results based on the facts achieved
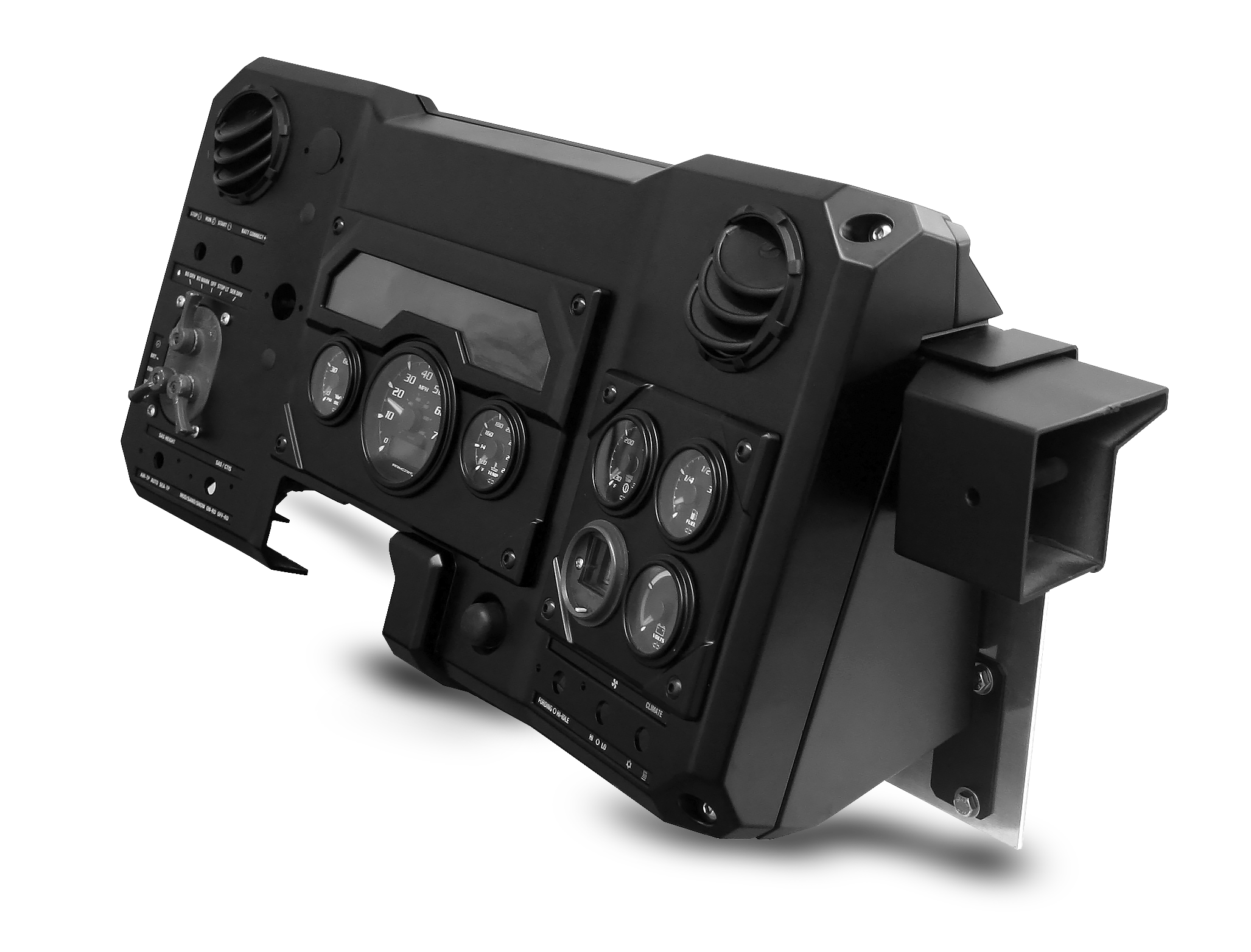
Reverse Engineering
Reverse engineering is the process of analyzing a component or system to:
- Identify the system of interrelationships
- Create representations of the system in another form – CAD
- Create the physical representation of that system – CAM
Reasons to reverse engineer:
- The original manufacturer of a product no longer produces a product or is unable or unwilling to provide additional parts or demands inflated costs for sole-source parts
- To update obsolete materials or manufacturing processes with more current, less-expensive technologies
- There is inadequate documentation of the original design
- The original manufacturer no longer exists, but the customer needs the product
- The original design documentation has been lost or never existed or the original CAD model is not sufficient to support modifications or current manufacturing methods
GD&T and Dimensional Management
Geometric dimensioning and tolerancing for new legacy products
- ASME Geometric Dimensioning and Tolerancing Professional (Y14.5) Certification
- Datum / Locator selection, coordination, optimization and strategy
- Development and identification of key product critical characteristics
- Tolerance optimization
Design of experiments and statistical analysis
- Process optimization
- 3-D and 1-D variation analysis
- Process capability analysis and statistical process control
- First-time quality through robust design and predictive analysis
Cost of quality analysis
Product and process root cause analysis
Measurement plan development and measurement collection consultation
- Measurement gauge design and validation
- Coordinate measuring machine (CMM) strategy
- Data analysis and coordination
Design for manufacturing / assembly
- Assembly tooling and fixture design
- Weld tooling design and distortion analysis
- Part to part interface, design and analysis
Training
- Quality Systems, Dimensional Management & Geometric Dimensioning and Tolerancing ASME Y14.5M
Prototyping
We can produce prototypes for a variety of needs:- Conceptualization
- Fixture tooling design
- Form and fit verification
- Low volume production runs
- Manufacturing aids
- Marketing presentations
- Materials selection
- Production tooling
Traditional Prototying
- NC/CNC milling
- NC/CNC turning
- EDM
- Sheet metal
- Plastic molding
- Ferrous and non-ferrous casting
Rapid prototyping
- Stereolithography (SLA)
- Urethane casting
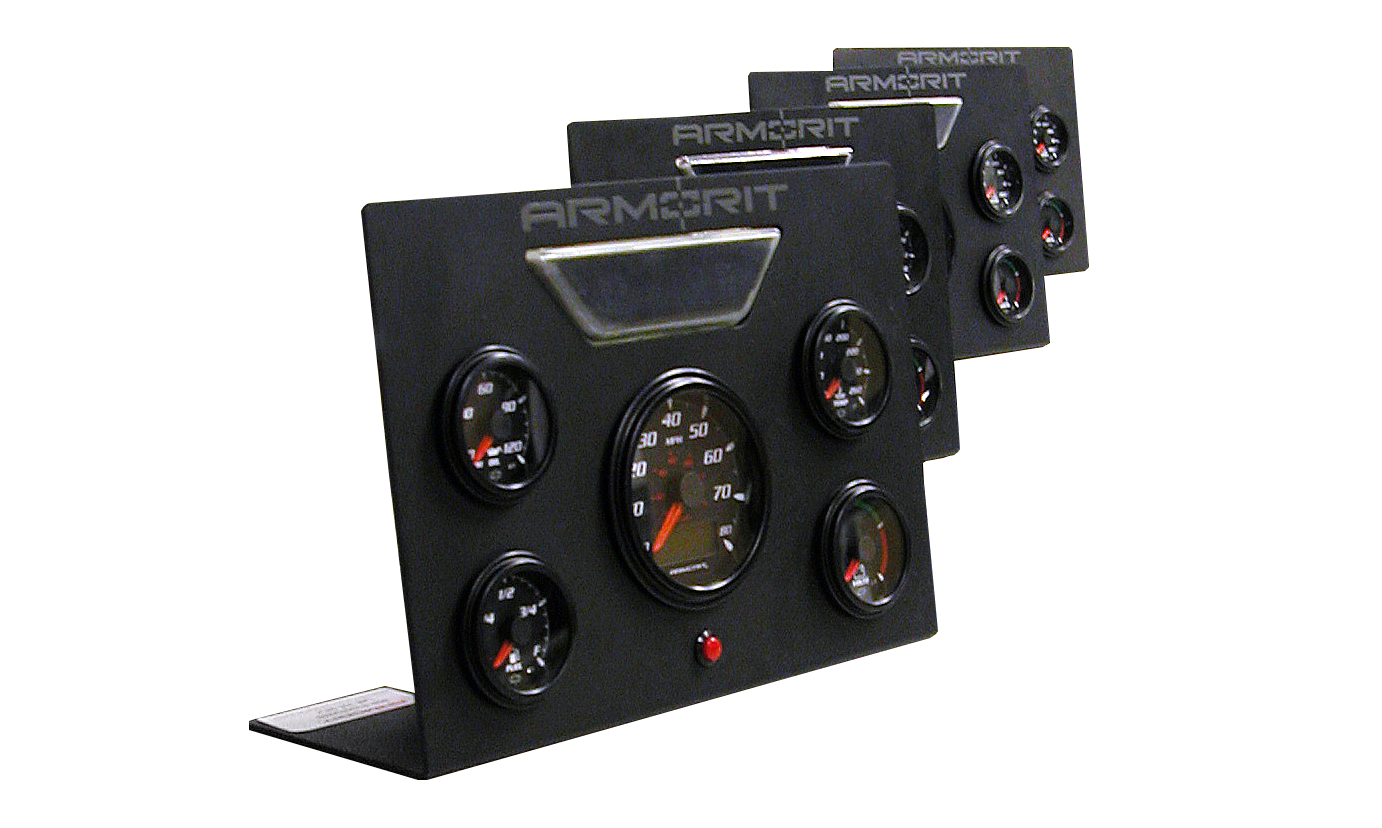
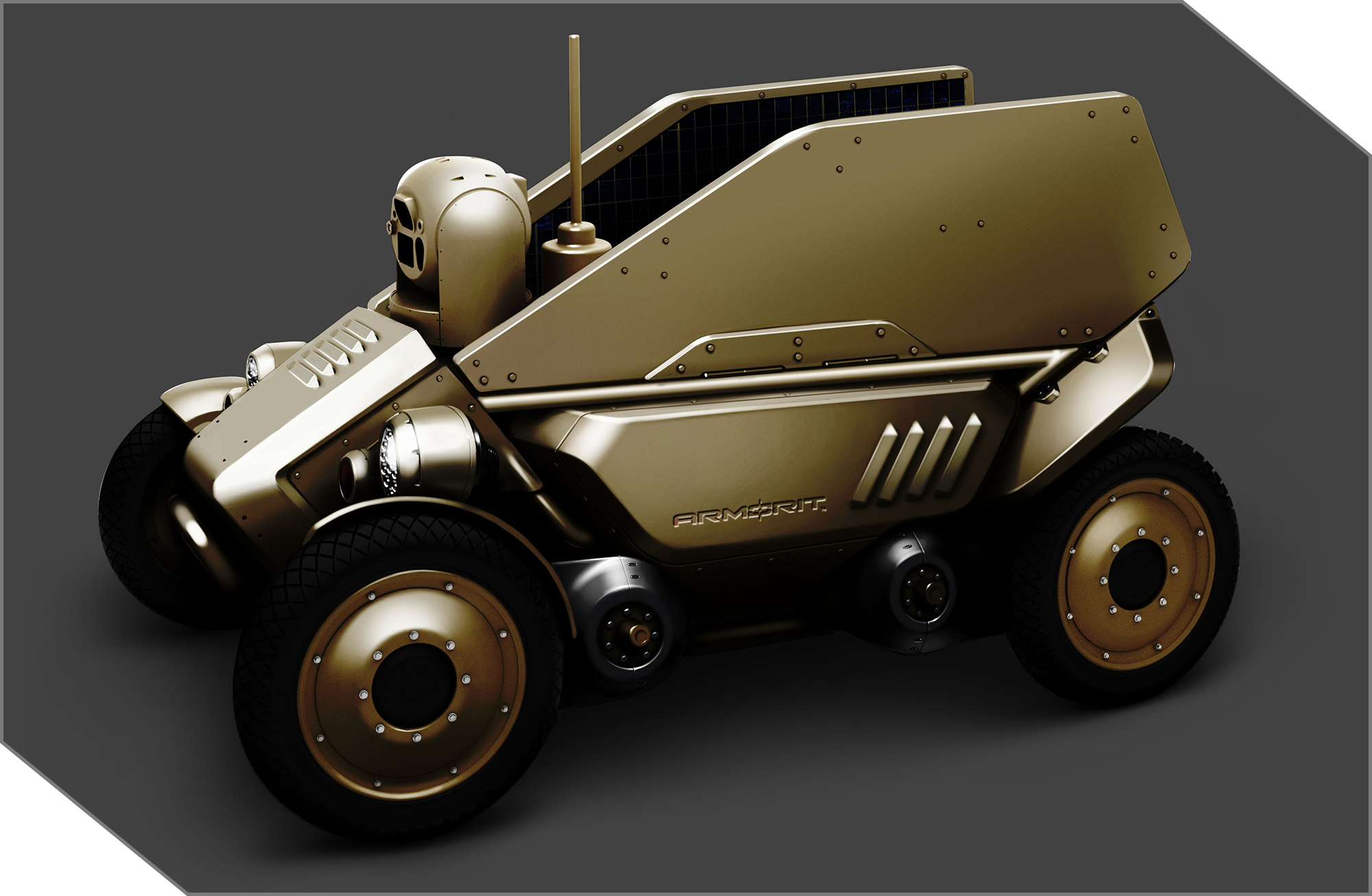
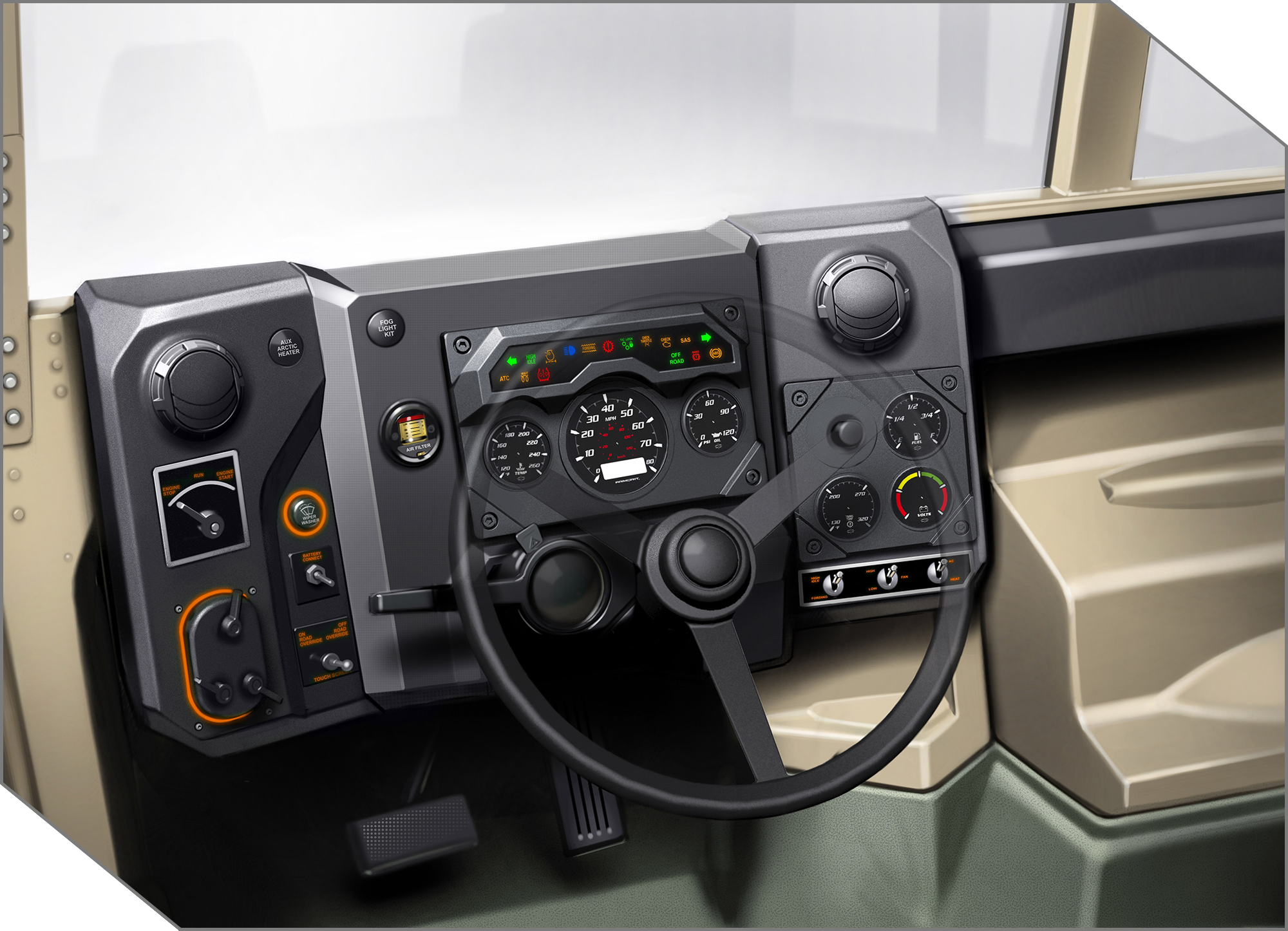
Systems engineering and Integration
is helping our customers achieve new levels of performance, with innovative ideas, better practices and cost improvements.Expertise
Our Systems Integration approach is comprised of electrical, mechanical, industrial, graphic, and software engineering disciplines with focus on their integrations into product development, manufacturing assembly, delivery and life cycle support. We combine knowledge, education and experience to offer practical solutions for your systems integration challenges. Our objective is clearly defined: To provide technical expertise for the most cost-effective implementation of product development, implementation, delivery and support.
From Theory to Implementation
Analytical studies are performed to evaluate system component interactions to aid development of specifications for medium to small systems and sub-systems. Analyses done prior to a new installation or legacy upgrades can avoid lengthy development and implementation cycles. On-going technical support is provided through collaboration, training programs, publications and on-site consultations.
One Stop Solution
Whether you are designing, upgrading or evaluating cost reduction opportunities, our systems integration approaches and people have the experience, expertise and technology to assist with engineering and delivery for your new or legacy products. We can provide complete analysis services that include on-site investigations, quantifiable product and cost improvement opportunities, root cause analysis, measurement equipment and studies and commitment to quality and delivery.